Impianto di verniciatura Sandvik - Nastro trasportatore
Nastro trasportatore per impianto di verniciatura Sandvik
Da quasi 150 anni, il nome Sandvik è sinonimo di qualità, con un fatturato annuo di 89 miliardi di corone svedesi e 47.000 dipendenti in tutto il mondo. Lo stabilimento Sandvik Construction and Mining di Ballygawley, nella contea di Tyrone, è oggi il centro di eccellenza per la produzione di attrezzature mobili di frantumazione e vagliatura utilizzate nell'industria mineraria e estrattiva di tutto il mondo.
Con l'ampliamento pianificato dell'attuale stabilimento produttivo di Ballygawley, Sandvik ha riconosciuto la necessità di un nuovo impianto di finitura che includesse cabine di granigliatura, cabine di verniciatura, forni e un sistema di trasporto automatizzato per semplificare questa parte del processo produttivo e far fronte alla domanda in costante aumento di macchine.
Collaborando a stretto contatto con gli ingegneri di Sandvik e altri importanti appaltatori associati, Amber Industries Ltd ha sviluppato una soluzione chiavi in mano e si è successivamente aggiudicata l'appalto per il nuovo sistema di trasporto che utilizza il nostro trasportatore aereo standard Autotrack 500M Power & Free.
I requisiti
Il briefing fornito da Sandvik prevedeva che il sistema di trasporto dovesse gestire tutti i derivati dei componenti di frantumazione e vagliatura, con un peso fino a 3000 kg e una lunghezza di circa 8000 mm. Un requisito fondamentale del sistema di trasporto era la possibilità di caricare e scaricare facilmente questi componenti lunghi e pesanti e, una volta caricati in sicurezza, di trasportarli automaticamente attraverso vari impianti e attrezzature, a volte dovendo rimanere fermi mentre in altre aree del processo il prodotto era in continuo movimento.
Per soddisfare tutti i requisiti di Sandvik, il sistema è stato progettato con 2 sezioni di caduta lunghe 9000 mm, una situata nell'area di carico e una nell'area di scarico. La stazione di carico è dotata di un gruppo di barre di scorrimento vuote fisse in posizione che consente all'operatore di abbassare la barra di scorrimento sul carrello della sezione di caduta, adattandosi al percorso del nastro trasportatore fino a un'altezza di carico ergonomicamente idonea.
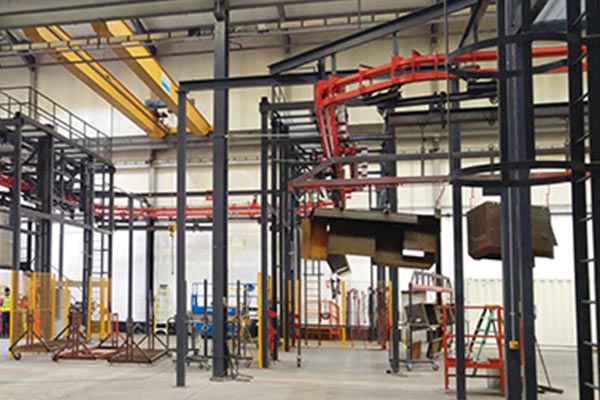
La barra di volo e il prodotto vengono quindi trasferiti dalla catena di distribuzione più veloce a una catena di processo più lenta, dove il prodotto viaggia continuamente a un passo dato attraverso una cabina di primerizzazione e poi attraverso un forno di polimerizzazione verde per un periodo di tempo e una temperatura stabiliti.
Dopo la polimerizzazione verde e l'appassimento, lo strato superiore viene applicato attraverso una seconda cabina di verniciatura a polvere che a sua volta passa attraverso il forno di polimerizzazione principale per la polimerizzazione finale a una temperatura di 220 gradi centigradi per un periodo di tempo stabilito.
Come parte del sistema, il trasportatore è dotato di un dispositivo di arresto della produzione dotato di un segnale semaforico che indica se il trasportatore è stato arrestato per scopi di produzione o per un arresto di emergenza.
Questa funzione consente agli operatori di arrestare il trasportatore di processo, consentendo al contempo al trasportatore di consegna (catena veloce) di continuare a funzionare, il che di fatto continua a mantenere le operazioni di scarico senza dover arrestare l'intero impianto.
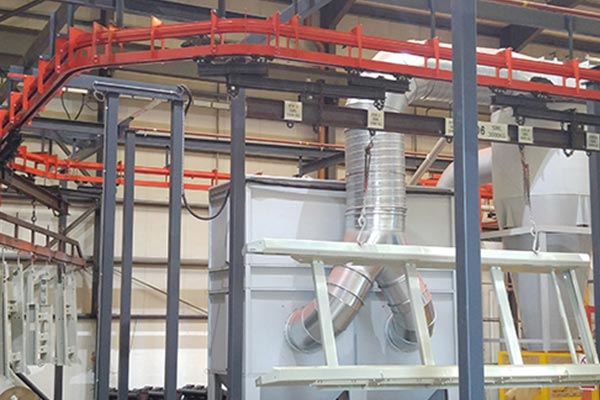
Lo scarico del prodotto, come per il carico, avviene tramite una seconda sezione di caduta lunga 9000 mm che consente agli operatori di abbassare il prodotto verniciato finito e fermo fino a un'altezza di scarico adeguata. Una volta rimosso il prodotto, la barra di volo vuota risale a un livello superiore e viene trasportata nuovamente alla sezione di caduta del carico. Le sezioni di caduta sono dotate di saracinesche di controllo per garantire la rimozione sicura del prodotto. I principali vantaggi delle sezioni di caduta hanno garantito che l'abbassamento del prodotto potesse essere ottenuto in un'area ridotta rispetto a quella di un tradizionale sistema di trasporto a nastro. Il fatto che la barra di volo ferma possa essere abbassata fino a un'altezza di carico e scarico adeguata si è rivelato vantaggioso per gli operatori, poiché si adatta alle diverse dimensioni dei prodotti da gestire.
L'utilizzo di componenti elettronici all'avanguardia consente l'integrazione del sistema di trasporto con altri impianti e attrezzature, garantendo la corretta movimentazione e tempistica dei prodotti, ove necessario. Il sistema di controllo principale è dotato di un sistema di accesso remoto che consente agli ingegneri software di Amber Industries Ltd di accedere al sistema dal nostro stabilimento di produzione di Oldham, nel Lancashire.
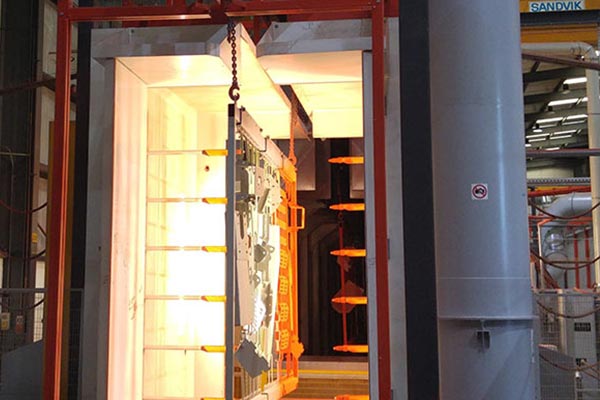